Deformable elements such as cables, hoses, wires, and ropes are involved in several applications both in domestic and industrial scenarios: just think about tying the laces of your shoes, or plugging the charger of your mobile phone, or wiring all the cables inside your computer or your car. In particular, cables are widely employed in the automotive and aerospace industries, especially in routing operations. In industrial frameworks, cables manipulation is usually carried out by human operators, representing a bottleneck for several applications. The automation of these operations would hence bring considerable economic benefits and relieve operators from these repetitive tasks. However, granting robots to properly manipulate cables is challenging due to the complex modeling of the deformation of these elements and to the non-trivial description and sensing of their shape.
Figure 1 shows an example of cable routing operation, where specific portions of the cable must be clipped into some fixtures to enforce a desired shape.
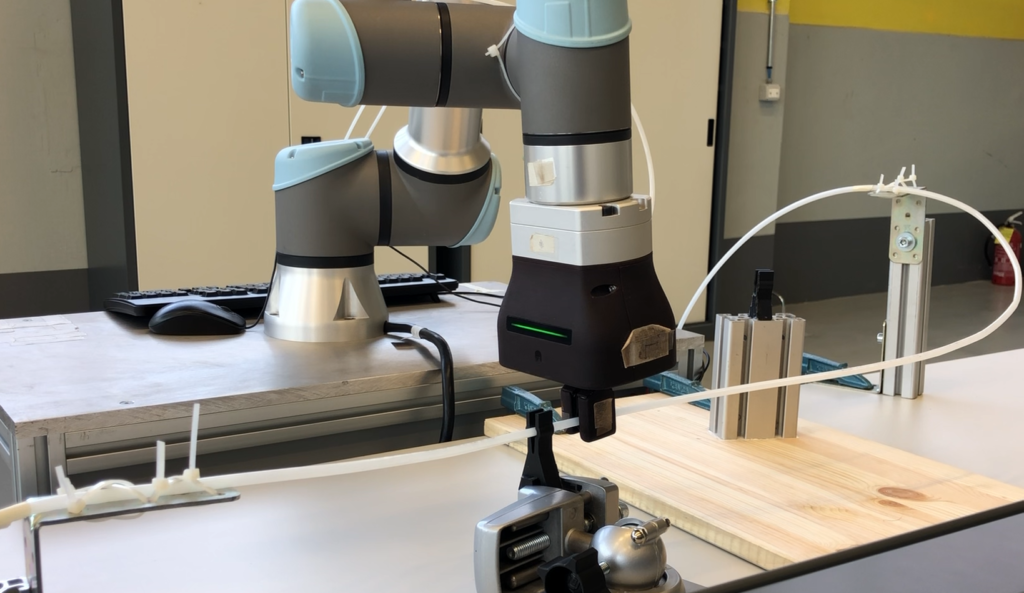
Industrial operations usually involve quite rigid cables, already constrained at their extremities (as shown in Figure 1). To robotize cable routing operations in our research we have defined a strategy to estimate the local shape of the grasped cable using tactile sensors mounted on the gripper fingertips. The robot first aligns the fingertips with the estimated local shape of the cable, roughly known, grasps it and then follows the unknown contour of the cable in the 3D space. In the meanwhile, the robot keeps track of the traversed distance along the cable to identify and insert predefined portions of cable in intermediate clips whose poses are known. Since the cable is stiff, the ability to follow its contour allows it to adapt to its natural 3D shape without the risk of straightening and damaging it during the operation. Cable contour following is challenging as the cable’s shape varies dynamically while the robot follows its profile. The techniques applied to perform contour following of rigid objects cannot be directly applied. We hence exploit capacitive tactile sensors on both fingertips mounted on the Smart Gripper manufactured by Camozzi Automation.
A capacitive tactile sensor relies on the same working principle of a parallel plate capacitor and consists of two main elements, as shown in Figure 2. The first element is a matrix of taxels, representing the lower plate of the capacitor. The second element is composed of a dielectric layer directly in contact with the mentioned taxels, and of a soft upper conductive layer, representing the other plate of the capacitor. The output of each taxel is a measurement of the capacitance depending on the distance between the external layers. When an object touches the skin, the soft dielectric is deformed, and the sensed capacitance increases as the distance between the layers is reduced.
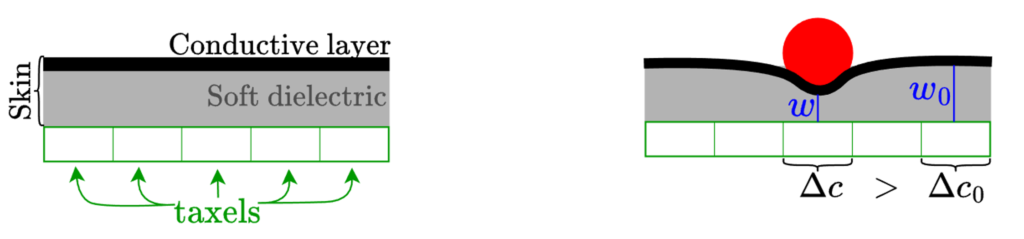
Tactile perception allows indeed to reconstruct the local shape of the cable and to compute an estimate of the future one. This information can be exploited to manipulate the cable without estimating its entire shape at once.
When the cable is manipulated, two kinds of misalignment can arise: a planar misalignment and an axial misalignment. Analyzing the output of the tactile sensors, it is possible to estimate these parameters and determine the actual configuration of the grasped cable.
The robot is controlled to slide along the cable to perform cable routing operations while compensating for the estimated misalignment. Moreover, the sliding velocity along the cable is adaptively modified depending on the estimated parameters describing its shape: the larger the misalignment, the smaller the displacement of the robot along the predicted shape. Consequently, the robot can quickly follow the contour if the cable is straight. Furthermore, it can recognize and adapt to considerable curvatures since it compensates for the estimated misalignment moving slowly and in small steps, repeating this procedure all along the curve.
References:
- A. Monguzzi, M. Pelosi, A.M. Zanchettin, P. Rocco – “Tactile based robotic skills for cable routing operations”, 2023 International Conference on Robotics and Automation (ICRA). IEEE, 2023.
- J. Sanchez, J. A. Corrales, B. C. Bouzgarrou, Y. Mezouar– “Robotic manipulation and sensing of deformable objects in domestic and industrial applications: a survey”, The International Journal of Robotics Research, 2018.
- J. Zhu, A. Cherubini, C. Dune, D. Navarro-Alarcon, F. Alambeigi, D. Berenson, F. Ficuciello, K. Harada, J. Kober, X. Li, J. Pan, W. Yuan, M. Gienger – “Challenges and outlook in robotic manipulation of deformable objects”. IEEE Robotics & Automation Magazine, 2022.