One of the benefits arising from the adoption of collaborative robots is the possibility to share or carry the load during transportation or manipulation. This type of collaborative operation can clearly reduce the muscular effort of the human, and possibly increase the quality of working environment.
Musculoskeletal disorders (MSDs), in fact, represent one of the major work-related health problem in developed countries, affecting almost 50% of industrial workers. As MSDs are mainly due to strenuous biomechanical solicitations due, e.g. to payload transportation or bad postures, it is widely agreed that collaborative robots can help in preserving employees’ health by taking up physically demanding tasks which are too complex to be fully automated.
There are several factors influencing the ergonomic assessment of a certain pose. The most crucial ones are certainly the body posture, which might lead to severe static joint load, the payload or the external force exerted on the musculoskeletal system and the rapidity of the motion, e.g. the presence of large accelerations. Differently from other works in which the robot simply acts as a passive positioner, a proper motion of the robot is proposed in order to mitigate this effect.
The key idea is then to move the robot proportionally to the displacement of the human with respect to the ergonomic reference posture. By doing so, we expect the human to compensate for this movement by moving towards a more ergonomic posture.
At Politecnico di Milano, we developed and applied this concept to a spray painting task of a car bumper. Differently from the case of car production, in an aftermarket scenario this task is hard to be fully automated, due to the high variability of parts being manipulated.
The relationship between the average value of displacement from the ergonomic posture and the amount of assistance given by the robot is an important KPI (key performance indicator). A correlation analysis shown that these two quantities are negatively correlated.
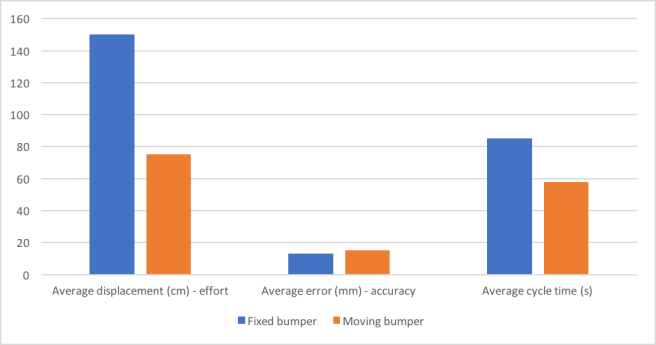
Another important indicator, which is more related to the usability of the application, is the accuracy of the operator in performing the given task while the robot is moving. Quite surprisingly, the average accuracy is not significantly influenced by the motion of the robot. Finally, beside the postural and the accuracy analyses, an important performance indicator is the time required to perform the prescribed task by the collaborative system, which has been reduced by around 25%.
To summarise the outcomes of the experimental campaign, we can clearly state that the intelligent object handling strategy introduced in this work is responsible for:
- smaller motions of the tool handled by the operator;
- approximately the same level of accuracy in executing the task;
- shorter cycle times for the collaborative painting operation
which clearly result in a better productivity, a lower exposition to musculoskeletal disorders and, in turn, no substantial modification in the quality of the produced good.
References:
- A.M. Zanchettin, E. Lotano, P. Rocco – “Collaborative Robot Assistant for the Ergonomic Manipulation of Cumbersome Objects”, IEEE/RSJ International Conference on Intelligent Robots and Systems, IROS 2019, Macau, November 4th-8th, 2019.
- OSH in figures: Work-related musculoskeletal disorders in the EU – Facts and figures, http://osha.europa.eu/.
- P. Maurice, V. Padois, Y. Measson, and P. Bidaud, “A digital human tool for guiding the ergonomic design of collaborative robots,” in 4th International Digital Human Modeling Symposium (DHM 2016), 2016.